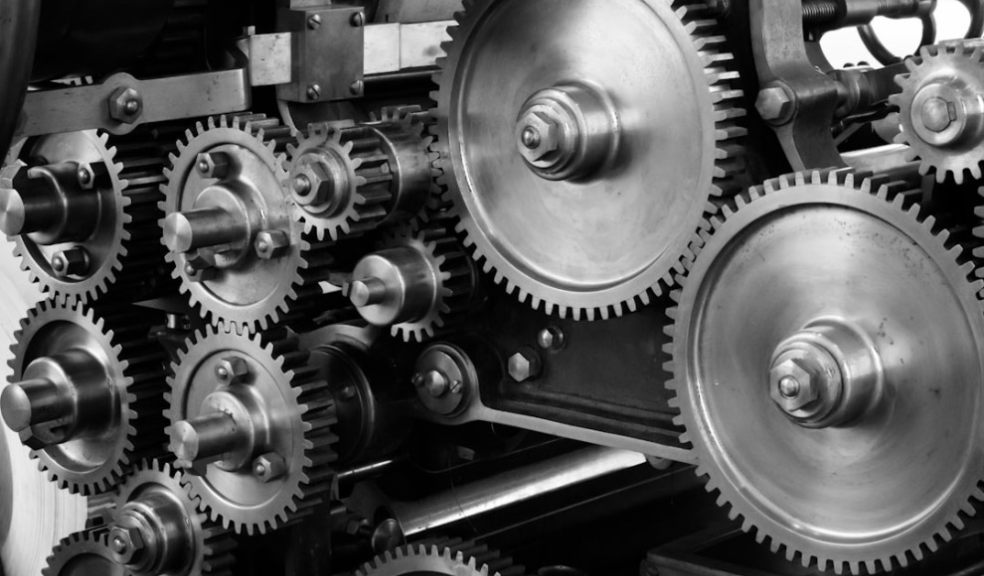
How turning is the base of mechanical components: tools, materials and applications
Turning forms the base of many mechanical parts used in sectors like aerospace or automotive components: it’s a critical process that creates some essential parts in motors and aeroplanes. Depending on how you utilise the process, it can make several different components. Look deeper into this process and see its tools, materials, and applications.
What’s turning?
Imagine you see a workpiece mounted on an axis which rotates, with another tool removing material from it as it spins. That’s the machining process called “turning”, which uses a turning machine or lathe to complete the process. Companies like A&B Torneria will use only the best machines for this process.
The turning machine can be programmed to work on different angles, geometries and materials. This process allows manufacturers to make multiple components with high tolerances. It also creates the ideal surface finish. These workpieces are called turned parts or machined components.
Tools
While this process is underway, it uses various tools. The single-point cutting tools carefully cut away material from the workpiece. The design of the machine can vary depending on the type of machined component it creates.
If you use a CNC (Computer Numerical Control) process, then it uses CNC-enabled turning machines or lathes. This process is ideal for creating engine, turret or special-purpose lathes. The following tools are also necessary:
- Chuck: holds the workpiece while it spins;
- Tailstock: supports the workpiece’s end when turning between centres;
- Feed mechanism: controls the speed by which the cutting tool moves.
Materials
This operation is available for a wide range of materials. The most common ones are aluminium, steel, brass, nickel alloy, titanium and plastics. The plastics include polycarbonate, nylon, PEEK, PEI, POM and ABS among others.
However, you can adjust the operation to the material, which means turning options like wood and other materials are also possible. The most significant component of this process is changing the speed, power, and cutting force to fit the material.
Process types
There are multiple turning processes, such as:
- Straight, taper or thread turning
- Facing
- Grooving
- Parting
- Boring
- Drilling
- Knurling
- CNC
Top applications for products
You can create various products using this process. Machined components you manufacture using result in axisymmetrical, rotational parts for the most part. The parts can boast grooves, holes, tapers, contoured surfaces and other features.
Standard automotive maintenance and construction parts are knurled inserts, knuts, threaded fittings, pinions, fixed plungers, ferrules, and hose fittings. These products are used in a car’s electrical and ABS boxes, HVAC, pressure switches, diesel, petrol and gas injectors among other things.
However, it also has use in various other sectors, like housing, security, medical, sports and industrial parts:
- Fittings
- Couplings
- Threaded nuts
- Measuring ferrules
- Threaded terminals
- Control rods
- Shutters
- Spark plugs
- Clutch shafts
Developing tailor-made solutions
Turning is a critical operation that develops parts used in everyday products like vehicles, sports equipment, musical instruments and furniture. It’s a crucial process that forms the base of mechanical components, as it often keeps these parts together and secure.