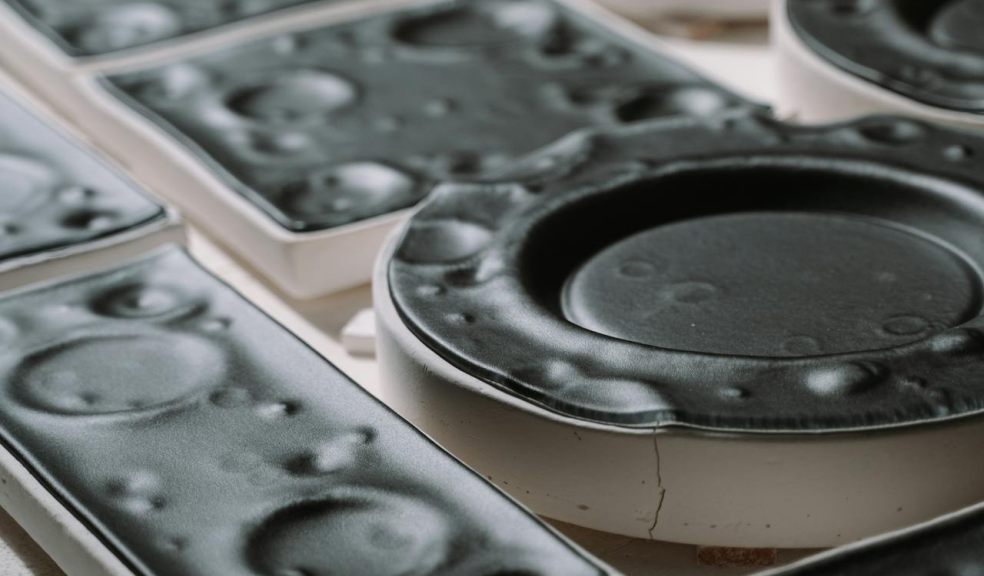
Top 5 Parameters That Affect Injection Molding Quality
If you're involved in manufacturing plastic parts, you already know how essential plastic injection molding manufacturing is. It's fast, scalable, and precise—making it one of the most widely used processes in the plastic industry. But here's the catch: even the most advanced molding machine can't guarantee quality if your process parameters are off.
Product defects like warping, sink marks, or short shots often trace back to how the process was set. That’s why understanding and controlling key parameters is critical.
In this blog, you’ll learn about the top 5 parameters that directly affect injection molding quality—so you can reduce waste, boost consistency, and create high-performance parts.
1. Melt Temperature
Melt temperature is the temperature at which the plastic material becomes fluid enough to be injected into the mold. Get it wrong, and you risk part failure.
-
Too low? The plastic won’t flow properly, leading to incomplete fills or weak weld lines.
-
Too high? It can degrade the material, cause discoloration, or lead to flashing.
What can you do? Always check the recommended processing range for your specific resin. Adjust your barrel heater zones to stay within that range. Also, use a melt temperature probe rather than relying solely on machine settings.
Tip: Even a few degrees variation can affect flow characteristics. So if your part has thin walls or complex geometry, pay close attention.
2. Injection Pressure
Injection pressure is the force that pushes the molten plastic into the mold cavity. It directly affects how well the material fills every detail.
-
Low pressure may result in short shots or poor surface finish.
-
Excessive pressure can flash the mold or cause part stress and warping later on.
The key is finding the balance—enough pressure to fill the mold quickly and fully, but not so much that you damage the tool or part.
To optimize pressure:
-
Monitor fill time and adjust pressure incrementally.
-
Look for visual signs on parts (e.g., flashing or voids).
-
Consider using a pressure profile that starts high and drops as the cavity fills.
3. Injection Speed
Injection speed (also called fill rate) controls how fast the molten plastic is pushed into the mold. And yes, speed matters.
A fast injection:
-
Reduces flow marks and weld lines.
-
Helps with packing in thin-walled parts.
But too fast:
-
Can cause jetting (a worm-like defect).
-
May trap air, leading to burn marks or voids.
Slower speeds:
-
Can help vent gases more effectively.
-
Improve dimensional control in thick parts.
It’s all about matching speed to part geometry and material. Use faster speeds for thin parts, but back off the throttle if you're seeing surface issues or air traps.
4. Cooling Time
You might think the hard work is done once the part is molded. Not quite. Cooling is one of the longest—and most critical—stages of the cycle.
-
Insufficient cooling can lead to warping, shrinkage, or ejection marks.
-
Excessive cooling wastes cycle time and reduces efficiency.
Most shrinkage happens during cooling, so controlling this phase can greatly improve dimensional accuracy.
Here's how to improve it:
-
Use efficient mold cooling channels and uniform wall thickness in your part design.
-
Monitor mold surface temperature.
-
Don’t just set arbitrary times—use data (like part temperature) to decide.
Bonus: Better cooling = shorter cycle times, which directly cuts costs.
5. Holding Pressure and Time
Once the mold is filled, you enter the “packing” or “holding” stage. This step compensates for material shrinkage and ensures the part remains dimensionally stable.
If holding pressure is:
-
Too low: You’ll get sink marks or voids.
-
Too high: You may overpack the part, causing internal stress or flash.
Likewise, holding time must be long enough to allow the gate to freeze and the material to solidify—but not longer than necessary.
To dial it in:
-
Measure part weight—when it stops increasing, you’ve reached optimal holding time.
-
Watch for visual signs like sink marks or bulging areas.
-
Combine pressure and time adjustments with gate design and size.
Conclusion
In injection molding manufacturing, small changes in melt temperature, pressure, or cooling time can make a significant difference in product quality. Whether you're working in-house or partnering with an injection molding company, understanding and controlling these critical parameters will give you a competitive edge.
Now that you understand these five critical parameters, take a look at your current setup. Are you dialing in each one with intention, or are you relying on defaults and guesswork? With a few smart adjustments, you can produce parts that are not just good—but exceptional.