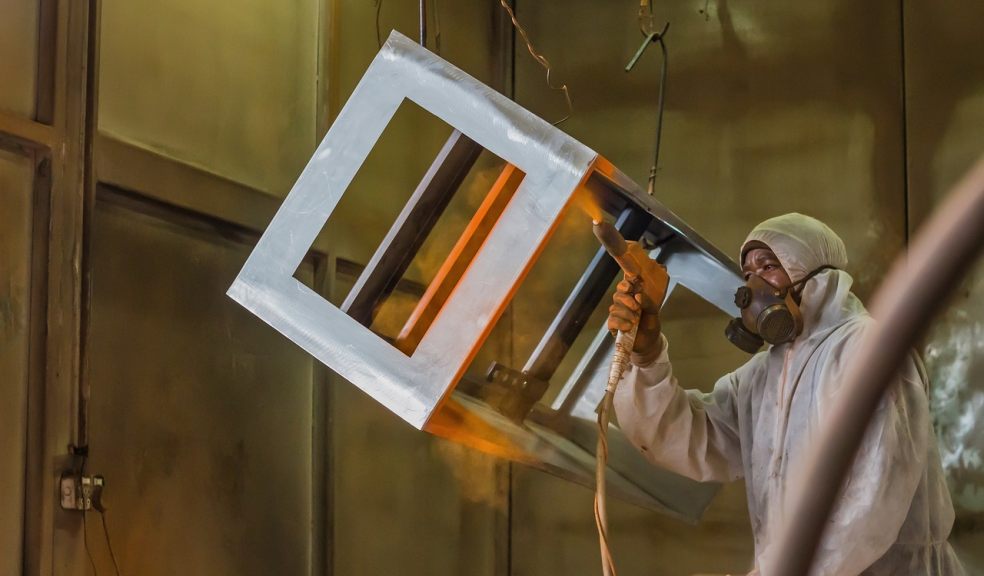
Choosing the Right Equipment for Your Home Finishing Project
Selecting the appropriate finishing equipment is key in creating happy customers and preventing dissatisfied ones.
Before powder coating can occur, metal parts must first be prepared by either etching or blasting to allow the coating to adhere securely. Accurate preparation processes will help avoid finish issues in the future. Finishing coating equipment can be expensive, but the outcome of a quality finish justifies the processes and cost.
1. Pre-treatment
Prep work is key to creating the ideal finish. While it may take more time up front, proper surface preparation will save time in the end by eliminating poor-quality finishes that cost more to correct later than they would if completed properly from the outset.
Powder coating requires pretreatment with either an etch or blast process or chemical pretreatments to ensure that powder can adhere securely, giving you durable exterior finishes and premium durability.
Before applying wood finishes, it is always a good idea to treat the surface with something that limits absorption (such as wood conditioner, sanding sealer or shellac thinned 50 percent). This will help your finish adhere to the surface without blotching and ringing later on and hang your piece for spraying so that you can smooth out runs more effectively.
2. Powder application
Many industrial products feature custom powder-coated finishes for added color, texture and protection. From appliances and furniture to tools, wheelchairs and car parts, powder coating gives manufacturers an opportunity to add color, texture and protection.
Electrostatically charged powder coating can be applied using a special spray gun to grounded metal components, adhering through electrostatic bonds to adhere to them more eco-friendly than traditional wet painting.
This method also eliminates run-off, dripping and sagging that could result in rejected pieces, while eliminating the need for surface primers.
Next step in surface preparation is cleaning. Blasting removes inorganic contaminants like welding smut and laser scale as well as organic matter such as rust and corrosion from surfaces using controlled pressure blasting.
Prep work can be accomplished either in a purpose-built booth or using homemade equipment like a box fan and furnace filter. To prevent overspray, shooting in an uncluttered space with adequate ways of collecting it should be prioritized; when spraying toxic fumes it's advisable to wear a mask in order to safeguard yourself against inhaling toxic fumes.
3. Curing
Curing is the final step of powder coating on steel or aluminum parts and makes them both tough and durable. This involves placing them into an oven where polymers melt together to form crosslinks; this step takes time but produces high quality finished products.
A bake chart is used by powder coaters to assess their process' conformance to curing requirements set out by their coating supplier. To cure properly, parts must be heated within the bake chart's specified cure window for their dwell time and within its specified curing window; any deviations could lead to incomplete curing and coating failure.
Routine temperature profiling provides finishing managers with invaluable process information that helps ensure quality; troubleshoot efficiently and cost effectively; reduce waste, scrap, and fuel costs; as well as prove compliance. Modern temperature profiling technology includes a datalogger, transducer interface and thermal barrier which travels with the test sample through the oven while recording temperatures along the way; analysis software then transforms this profile into index of cure data.
4. Finishing
Finishing is the process of altering the surface of a manufactured part or product to achieve specific characteristics, such as aesthetics, adhesion, solderability, corrosion or tarnish resistance, hardness, flaw removal and/or electrical conductivity.
Applying the wrong powder coating could damage a product and alter its aesthetic; to prevent this from happening, it is crucial that as much information about both customers and products can be gathered prior to beginning this process.
Job shops or independent coating service contractors provide manufacturers who lack the capacity to complete metal finishing in-house with an ideal alternative. These businesses specialise in various powder coating technologies and offer prototype, short run and high volume production capabilities as well as expert technical support, troubleshooting and training services for their customers. When using solvents during finishing operations it is imperative that chemical resistant gloves such as nitrile or thick neoprene gloves be worn - thin vinyl and latex will only offer short-term protection so using thicker varieties would provide long-term protection - this option should provide adequate hand protection from harmful solvents for longer.