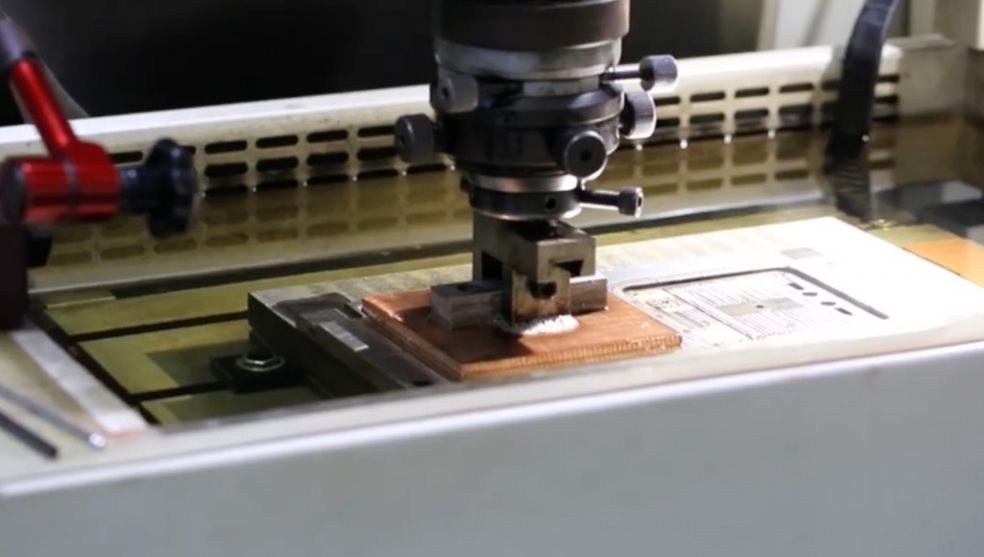
Plastic mold manufacturing - primary benefits to know
It is fascinating to know that plastic injection molding is known as a beneficial manufacturing method for producing different parts or products. This method is known as one of the most widely used manufacturing processes in the world for mass-producing plastic parts. What is plastic injection molding? Plastic injection molding is called as the process of manufacturing plastic parts as well as components from heating either plastic pellets or powdered plastics. After that, the liquid is forced into a mold to harden into the finished product.
Plastic injection molding comprises multiple advantages that other methods of plastic molding do not have. Here is the description of some of the significant benefits:
Super flexible in design
You will be surprised to know that Injection molded parts have a limitless amount of flexibility. No matters what the size of the produced parts? The reason is that injection molds are subjected to extremely high pressures, and the plastic within the molds is also pressed tighter than other molding processes.
Moreover, Computer aided design (CAD) and Computer-aided manufacturing (CAM) makes it possible to include minute details and intricate designs into the part's design, depending on the type of plastic used.
High efficiency in mass production
It takes a while to set up a machine, and once the injection molds have been designed to specification or the presses have been programmed, the molding process is very fast as compared to other molding methods.
It is essential to know that the plastic injection molding process can mass produce parts, all from a single mold. However, a high production output rate of plastic injection molding also allows it to be more cost-effective as well as efficient. Several online sites, such as qmolding.com, offers the best injection molding services.
Less expensive than plastic machining
It is essential to consider that the initial production of molds can be expensive at the cost of several thousand dollars. Once the shape is created, you are allowed to develop substantial quantities of plastic parts with minimal cost. However, an extensive series of plastic processing cost 25 times more than plastic injection molding. Moreover, plastic injection molding is among the most widely used plastic producing processes.
It is fascinating to know that the plastic injection process allows a unique option within applications where parts need to be persuasive or durable. Furthermore, it is possible to use fillers in the molds. The primary purpose of these fillers is to reduce the plastic's density while also adding greater strength to the molded part.
A smooth finished appearance
Do you know that plastic injection molding is a process in which the manufactured part has little or no finishing touch? The reason is that the shape of the collapsed section is closest to the finished appearance.
Moreover, simultaneous injection molding also allows concurrent use of multiple types of materials. Such as, you can add a filler to the hopper and add strength. It also allows you to change the properties of the plastic material according to your need and preference.
Lower labour costs
As the injection molding is an automated process, a majority of the process is performed by machines, computers, as well as robotics. It is fascinating to know that automation helps to reduce manufacturing costs through this lower labor cost.
Furthermore, post-production labour work is also minimal because the parts usually already a very finished look upon production. Here good news that most plastics can be recycled, and the injection molding process allows for recycled plastics. Due to the high tolerances on part molds, qmolding allows waste within the original manufacturing process.
The bottom line
Using injection molding ensures the parts manufactured hardly require any work after the production. The reason is that the parts have more or less a finished appearance after they have been ejected from the injection molds. Now, plastic injection molding is an environment-friendly process, and it's popping out day by day.