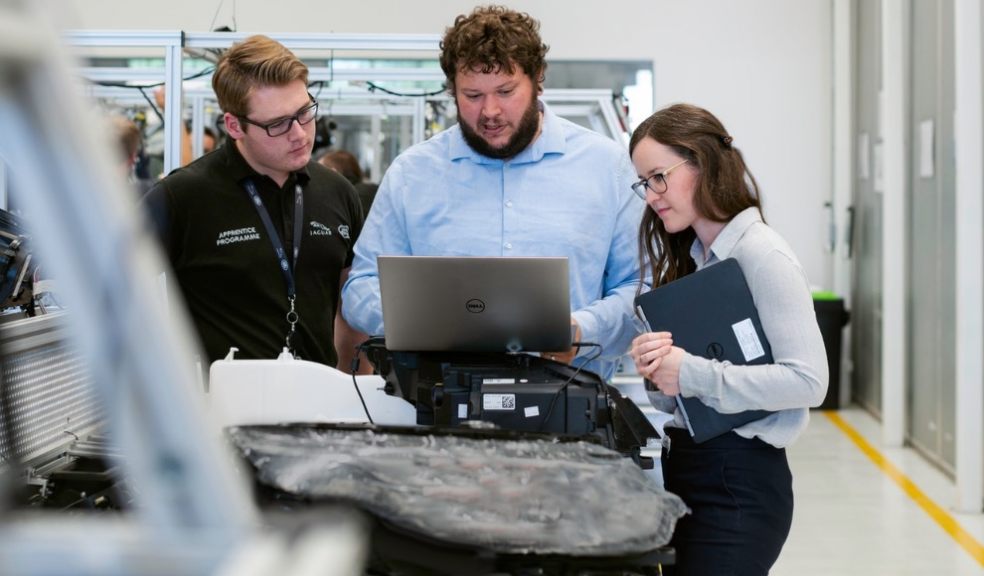
3 industries that benefit from remote monitoring systems
When many people hear “remote monitoring,” they think of the telescreens in 1984. However, remote monitoring has far more benign implications for a variety of industries that depend on environmental monitoring to safeguard public safety and comply with regulations.
Before the computer age, critical environmental conditions like temperature, pressure, humidity, or voltage would be measured by large analog machines that recorded conditions on strips of paper tape, with pens fluctuating to indicate changes in conditions. It was labor-intensive and inefficient to review all those meters of paper tape with human eyes, especially if you had to pinpoint the moment where a problem occurred due to changing conditions.
Modern data monitoring is handled much more efficiently by digital data loggers, where the conditional sensor—thermometer, barometer, voltmeter, etc.—is attached to a small computer processor, which records conditions on time-stamped entries in a digital drive.
There were limitations to this approach, as well. Users had to retrieve that data by USB or some other hard connection and then compile it into reports for compliance bureaus.
The advent of remote monitoring of environmental conditions was the true breakthrough, allowing conditions not only to be monitored constantly and accurately, but for the data to be pushed to the Cloud for automated compiling, adding those data loggers to the ever-expanding Internet of Things (IoT).
Remote monitoring also allows one unified, often cloud-based and automated “back office” to gather and compile data from a variety of sources into a centralized repository, accessible anywhere in the world.
More importantly for the users, remote monitoring also enables remote alerts. In the past, if the temperature in a cold supply chain suddenly spiked, suppliers might have no way of knowing that it had happened unless they had personnel on the premises, watching at all times. They might never know there was a problem until the whole inventory was ruined. The data logger could tell you when the temperature spike happened and how high it got, but the data logger could not turn back time and save the inventory.
Remote monitoring adds efficiency and agility to industries’ ability to protect their assets and inventory by communicating problems all over the globe. A Cloud-enabled data logger can send an alert to a manager’s smart phone if the temperature spikes—perhaps in time to deploy personnel and correct the problem before the asset or inventory is ruined.
Three industries in which this kind of remote monitoring have made a big difference include:
Healthcare
Nearly every vertical in the healthcare industry requires strict environmental monitoring for the safety of its consumers and to clear strict regulatory compliance hurdles.
It’s obvious why—we’re talking about pills that patients swallow or medications injected into their veins; devices that could heal them, diagnose them -- or hurt them in the event of a malfunction.
Patients convalescing may need to be kept in strict environmental conditions, while the machines used to manufacture the drugs and devices, or the devices themselves in service in hospitals and clinics, require strict operational environments.
Specific environmental monitoring considerations within the healthcare industry include:
- Pharmaceuticals. The raw materials used to make medications must be transported and stored properly, often within optimal temperatures and humidity conditions. The machines used to make and test drugs are sensitive, requiring exacting power conditions with careful attention paid to the pressure and voltage they are exposed to.
The manufacturing floor may have specific temperature, pressure, and humidity considerations. The finished medications must be stored and transported at proper temperatures, pressures, and humidities, sometimes maintaining a cold chain in the case of vaccines and live cultures.
- Medical Devices. Medical device manufacturers face many of the same considerations as pharmaceuticals. The manufacturing floor may have strict temperature and humidity requirements, the machinery strict voltage and shock pressure requirements. The finished devices must be stored and shipped in proper environmental conditions, including temperature and humidity, to ensure that they arrive functional.
- Laboratories. Laboratories may need to maintain optimal temperature, humidity, voltage, and equipment pressure to produce reliable results.
- Hospitals. Hospitals may need to maintain certain humidity and temperature for the safety of the patients and the operability of machines and devices on premises.
As Dickson notes, a healthcare organization may have many different monitoring points, making a centralized remote monitoring system ideal.
Food
The food industry also faces high hurdles of public trust. Without it, people wouldn’t eat at a restaurant or shop at a grocery store without wondering if the next bite might make them sick.
Maintaining the safety of the food supply is a complicated, multi-step process made easier by remote environmental monitoring at every vertical, including:
- Agriculture. The growing and harvesting of food products in the quantities required by the food industry requires careful attention to temperature, humidity, soil moisture, and weather patterns, all of which are enabled by remote monitoring.
- Processing. Food products must be processed at the correct temperature and humidity, while the power usage, voltage, and pressure of processing machinery is consistently maintained.
- Shipping and Storage. Food products must be stored and shipped at proper temperatures and humidities, often in a cold chain in the case of perishable products.
Since food production takes place over vast geographies, remote monitoring has added essential efficiencies to food production industries.
Aerospace
People and organizations depend on the aerospace industry to maintain the safety of commercial aviation—both for the shipping of goods and the transportation of people.
The aerospace industry also designs the rockets that, among other tasks, launch the satellites that enable remote monitoring, from weather satellites to GPS satellites.
Remote monitoring contributes to the aerospace industry in the form of:
- Monitoring the Manufacture of Components. Many aerospace equipment malfunctions can be attributed to faulty manufacturing. Aerospace manufacturing facilities must be monitored for temperature, pressure, humidity, and the pressure and power usage of manufacturing machinery.
- Monitoring of Components in Service. Planes and rockets must be monitored from afar to track their position, as well as exterior air temperature and fluid pressure under the wings and fins, fluid pressure and temperature inside of engines, and other key aircraft conditions.
Every component used in aerospace must comply with AS9100, an internationally-accepted manufacturing standard adapted from ISO 9001 and requiring strict environmental monitoring in the production of the components. Remote monitoring streamlines the compliance process.
Environmental monitoring played a huge role in the healthcare, food, and aerospace industries before the advent of remote monitoring. Remote monitoring technology makes the process much easier, more efficient, and automatic, reducing human error and catching problems early. Ultimately, this enhances the safety of these critical industries.